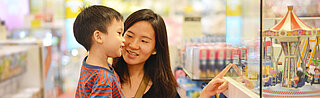
Toy manufacturing: Trends and status
Many years ago, Toy companies sourced from factories spread all across the globe. Then China opened up to the world, and a massive population of super hard-working people who were also very poor came into the global labour pool. Over time China became ‘the factory of the world’ and began to dominate consumer products manufacturing. Over the past two to three decades, China has accrued a huge capability for manufacturing, and manufactured billions of Toys for other countries.
Human nature suggests that we tend to expect the reality we have known to continue into the future. But the situation with China as the primary manufacturing hub for the world is changing for several reasons. This is affecting the Toy business now, but will also lead to further change across the next decade.
China’s economic miracle

Since the early 1980s, China has moved from being a poor agrarian economy to a modern economy. Poverty has been vastly reduced, and China’s economy is now the second biggest in the world with every chance of becoming the biggest economy.
Back in the 1980s, news reports from China’s major cities showed poor people wearing simple peasant clothing and cycling everywhere on bicycles. The city scenes we saw on the news back then did not tend to show high rise buildings or strong signs of urban growth. Fast forward to today, and China’s major cities are dominated by skyscrapers, automobiles and a modern affluent population.
The natural consequence of this economic advancement is that China is no longer the source of the world’s cheapest labour. Numerous other Asian countries now supply labour at much lower cost versus China. To put this in simple terms, due to increased labour costs, China today is arguably better placed to manufacture real cars versus Toy cars!
China’s demographic challenges
Much has been written of China’s demographic challenges. The birth rate in China has dropped to historic lows, but also young people are not embracing factory work in the same way as their parents’ generation did. Labour shortage is not a new issue in China’s toy factories. For many years, factories have seen a proportion of their workers go home for Chinese New Year and then not return to work afterwards. But the labour shortage has only intensified over time. The South China Morning Post reported that “By 2025 nearly 30 million manufacturing jobs in China will go unfilled, accounting for nearly half the jobs in the sector.” The same publication also quoted Cai Zhongpeng as saying that “Most of the workers in factories around the country are in their 40s and 50s, and it’s rare to see young manufacturing workers.”
The specifics of toy production
Why is labour so important though? Can’t these factories automate production to cut out the need for production? The answer to that question is that Toys often only get one selling cycle in the market, with as much as 70% of all Toys on sale every year being new to market. Therefore Toys lack the longevity historically required to justify investment in automation. Going forward, we will eventually get to the point wherever smarter artificial intelligence and more adaptable advanced robots can replace human labour, even in Toy production. However, at that stage there will not be much point manufacturing thousands of miles away from the key markets where the products will be selling. Presuming Technology removes the need for humans working on Toy production lines eventually. It’s most likely that the majority of Toy manufacturing or at least assembly will then happen primarily closer to the key markets of Europe and North America.
Geographic diversification of toy sourcing
Additionally, in an ever more complicated world, fear of geopolitical risk is also driving some production out of China. Those Toy companies who supply Mass Market retailers in the world’s biggest Toy market, the USA, have been told by those retailers to ensure that a significant amount of production is placed outside of China to reduce geopolitical risk. Major stock market listed companies are already sourcing circa 50% of their products from other countries towards the stated aim of ‘geographic diversification’.
Toy manufacturing: The new era has started

The current reality with regards to Toy production is that big companies are already sourcing from other countries as well as China. Vietnam, Indonesia and India are major beneficiaries in Asia. Mexico has seen a big surge in Toy production to supply the North American market. All of these geographies can offer cheap labour and capacity. The challenge though for Toy companies is that none of these geographies has the established supply chain for components and specialist materials that you can find abundantly in China’s manufacturing heartlands.
The factories in some of these places are also not used to working to the same standards of either production or communication as the excellent factories we have come to take for granted in China. In short, Sourcing from outside China is taking more time, causing frustration at inefficiencies and therefore taking up more management ‘head space’. These are not simple times. The easiest option by far is to keep on working with your long-established Chinese vendors, but taking the easy path is not always smart!
By way of a reality check, we also need to recognise that we are looking at a major trend in terms of Toy manufacturing reducing in China, but the country still manufactures the majority of the world’s Toys, and there is no evidence to suggest that China won’t still have a significant role going forward.
The evolution of China’s toy factories
The geographic shifts we are seeing for ‘OEM’ Toy manufacturing do not of course exclude China from having an ultra-significant role to play in the global Toy business. As the world’s second biggest Toy market, much production capacity is needed to supply the local market. Moreover, there is also a strong shift from producing other people’s Toys on an ‘OEM’ or ‘Contract Manufacturing’ basis to Toy factories seeking to move up the value chain and become Toy companies themselves. Normally those factories who have younger management who have not spent decades producing cheap Toys at low cost seem better equipped to adapt to all that being an export-oriented Toy company entails. Many Toy factories have evolved or are going to evolve from manufacturing $3 Toys to producing more complex items, like automobiles, planes, and other forms of more advanced products. The Toy industry is going to therefore lose a huge amount of expertise and domain knowledge in the next few years as some of our long serving suppliers move onwards and upwards. So as the global Toy industry moves back from a primary Sourcing hub model back to a multi-hub model, we should not expect an entirely smooth transition.
About the Author
Steve Reece has worked in the Toy business for 25 years. Having previously worked for Hasbro managing iconic brands such as Monopoly, Play-Doh and Trivial Pursuit, Steve now runs a Consultancy company – Kids Brand Insight – helping Toy companies grow export sales, build robust diversified supply chain and recruit the right people.